Casting is a method of production dating back to the 19th century. Certainly, over time, this technology has advanced and today we use modern machines. However, the basic procedure has not changed much. Today, we recognize several ways of casting in production – but the most commonly used are the investment casting process and metal die casting. So which method is better and more efficient?
What Is Casting?
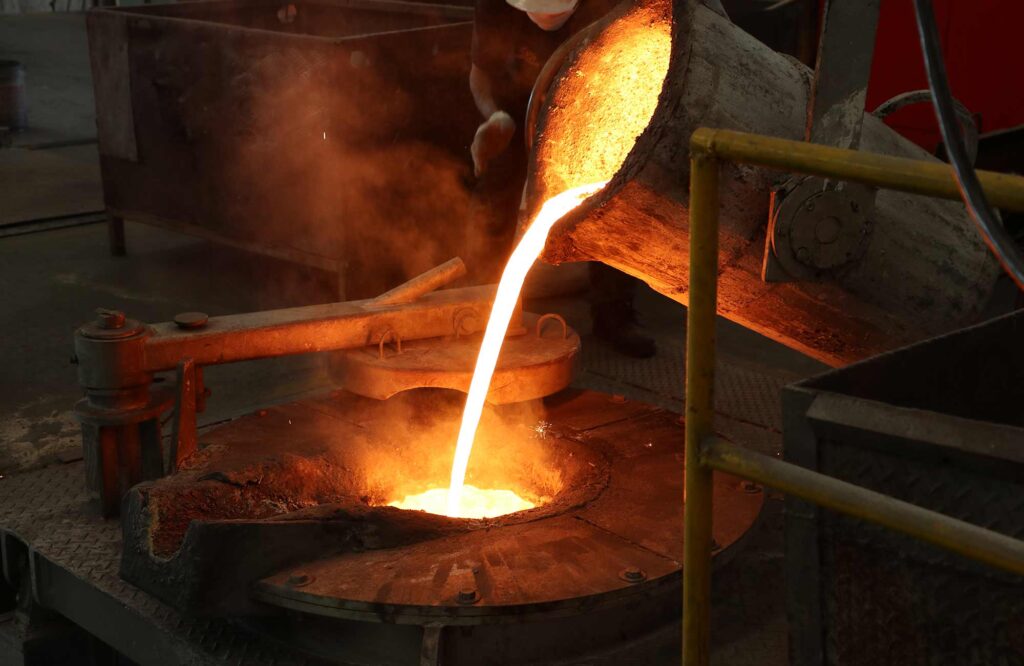
Casting is a technology of shaping metal objects by casting molten metal into molds – by using a model to obtain a casting after cooling. Casting is a very convenient process of making machine parts whose shape is complicated, with internal contours and irregular channels. Casting is also used for the more economical production of machine parts and elements. Modern technology and modern casting equipment enable the production of castings of different dimensions, accuracy, and surface quality. Thus, the need for subsequent mechanical processing is less and less present.
How Does Die Casting Function?
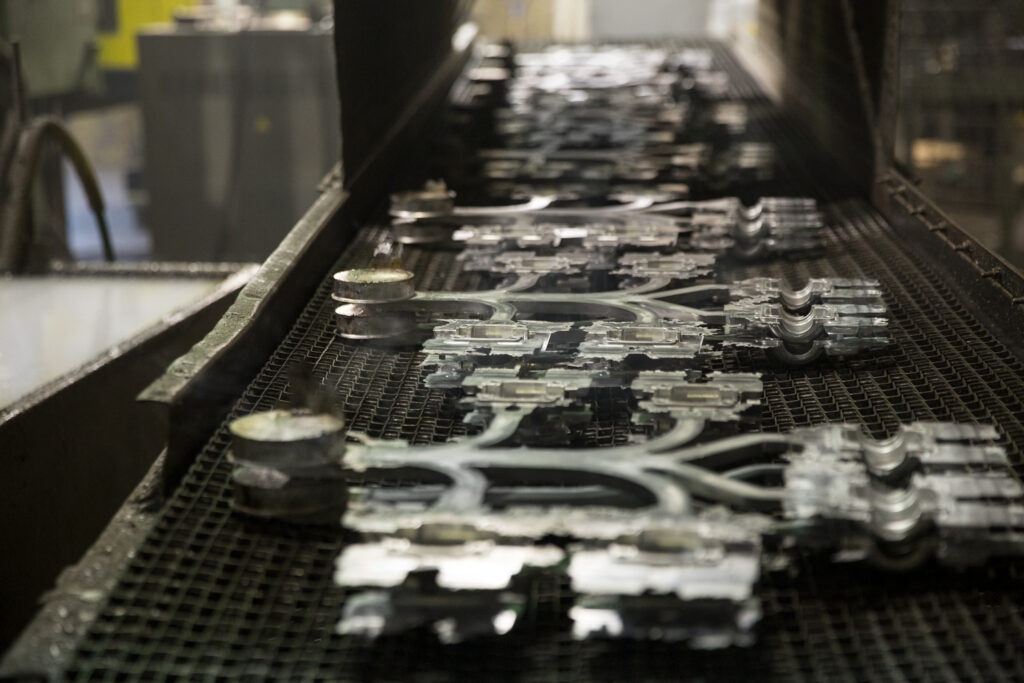
This method of casting is the most common process of producing parts made of metal. Namely, the molten metal is inserted into the mold under pressure. The molds themselves are usually made of hardened steel and can withstand extremely high temperatures. After the molten metal is poured into the mold, it is cooled and hardened – after which it is removed from the mold, and the process can be repeated. This is the simplest explanation of how die casting works. Certainly, some new technologies are applied within die casting, such as pouring into hot or cold chambers, etc. Standard hardened steel molds can be used on average more than 150,000 times for casting. The equipment for casting as well as metal die – are usually a capital investment and require a large amount of production.
Investment Casting Process
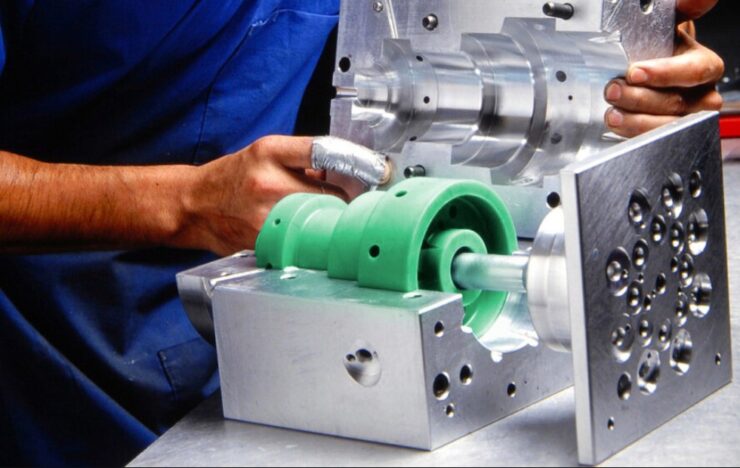
This process involves the production of parts using the so-called lost wax procedure. Although this procedure is longer, it has its justification. According to DaWangCasting, during this procedure, a wax prototype of the mold is made, which is then immersed in liquid ceramics. Once the ceramic hardens – you are left with a ceramic mold. In such a ceramic mold that can withstand high temperatures – molten metal is poured, that is, in the place where there used to be a wax prototype that melted. Once the metal has cooled and hardened – the ceramic mold breaks and discards leaving a perfect metal casting.
Investment Casting VS Metal Die Casting
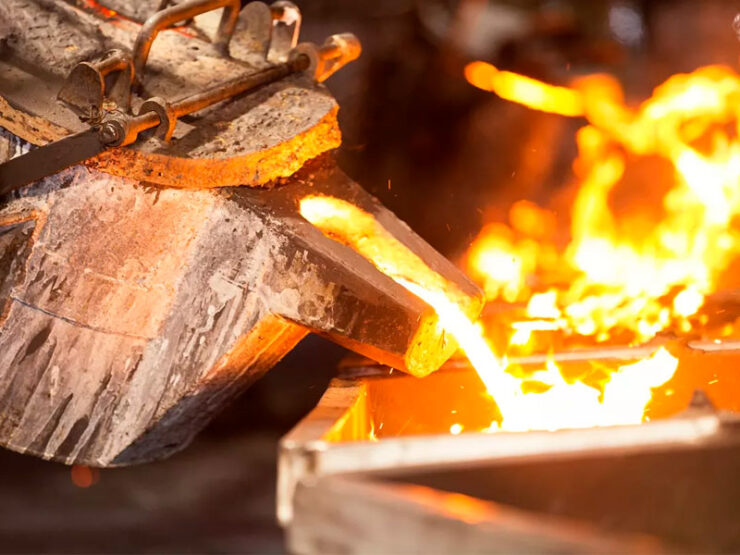
When it comes to deciding to apply one of these two methods – it is best not to oppose them at all. In fact, we need to look at all the advantages and disadvantages of both processes. In addition, we need to keep in mind the needs of our business, so we need to consider some key items such as the complexity of the design of the molds we make – or the materials and alloys we use in making them. Also, when deciding, we must consider the frequency of use and cost of tools. According to these parameters, everyone will individually decide which method is better and more cost-effective.
The Bottom Line
Although there are several casting procedures today, these are the two most commonly used. However, when comparing, we must keep in mind certain things related to production. If you still have not made a final decision – the advice is to always contact the professionals or the manufacturer with whom you will cooperate on this project.