The manufacturing sector is experiencing a technological renaissance, and at the forefront of this evolution is the increasing reliance on automation. Among the most transformative innovations is the rise of robotic welding systems. These automated solutions are redefining how industries approach fabrication, offering enhanced efficiency, safety, and accuracy.
Manufacturers across the globe are moving quickly to integrate robotic solutions. The demand for smarter production is no longer optional—it’s urgent and necessary.
Key Points
- Robotic welding increases efficiency, consistency, and accuracy in fabrication.
- Human error and fatigue are significantly reduced with automation.
- Robots can perform a wide range of welding methods across industries.
- Workplace safety improves by minimizing exposure to welding hazards.
- Initial investment is high, but long-term savings outweigh the costs.
- Proper integration planning is key to maximizing robotic system benefits.
Understanding Robots in Welding Applications
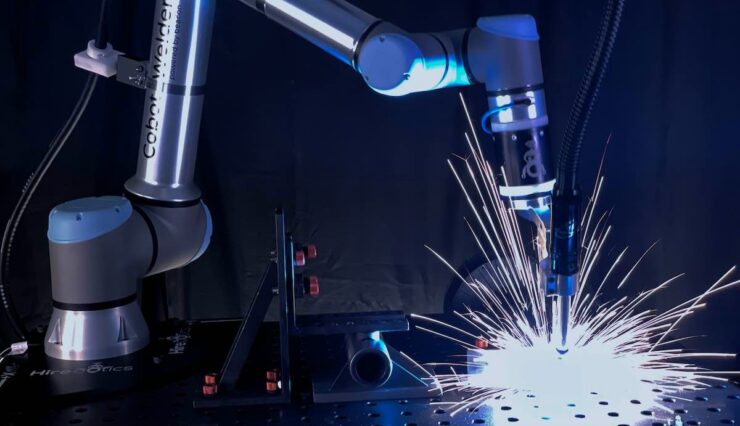
Robotic welding systems are automated machines programmed to perform welding operations with high precision and minimal human input. Typically, they feature robotic arms, welding torches, and sophisticated control software that guides the entire welding process. From basic assembly to intricate fabrication, these machines can execute a wide variety of welding methods such as MIG, TIG, arc, and spot welding.
What makes robotic welding particularly attractive is its ability to deliver consistent results. Human welders are subject to fatigue and variability, especially over long shifts. In contrast, robots can maintain accuracy over continuous runs, ensuring high-quality welds while reducing the risk of errors.
Industrial Benefits of Robotic Welding
Robotic welding is widely adopted in industries such as automotive, aerospace, construction, and general engineering. Its benefits extend well beyond simple productivity improvements:
- Efficiency Gains: Robotic systems can operate continuously with minimal downtime, significantly boosting production throughput.
- Superior Quality and Precision: Automation ensures consistent weld sizes, depths, and penetration, reducing defects and rework.
- Improved Workplace Safety: Removing humans from direct contact with welding hazards like fumes, sparks, and intense light enhances occupational safety.
- Long-Term Cost Reduction: Although initial investment can be substantial, savings from reduced labour costs, waste, and maintenance make robotic welding highly cost-effective in the long run.
Integrating Robots into Welding Processes
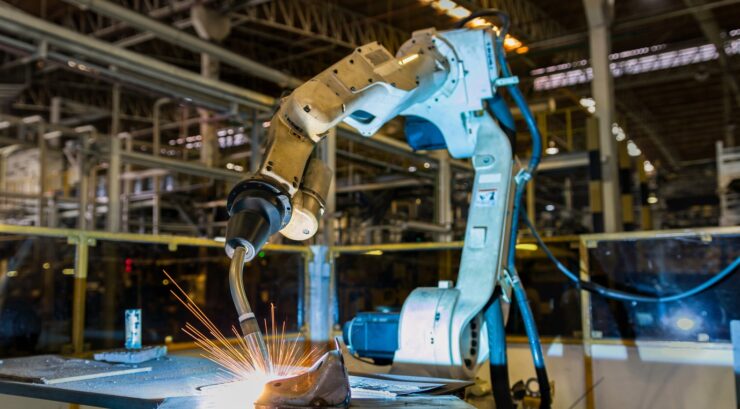
To get the most from robotic welding, it’s essential to plan integration carefully. Factors such as production volume, part complexity, and existing infrastructure must be considered. Collaborating with experts in automation ensures that the solution fits the specific requirements of your operation.
For businesses interested in learning more about the possibilities of robots and welding, Cyber-Weld offers comprehensive guidance and system integration services. Their experience in robotic welding solutions helps manufacturers streamline their processes and future-proof their operations.
Choosing the Right Robotic Welding System
Every manufacturing line has unique demands. Not all robotic welders are built for the same tasks. To get the highest return on investment, companies must identify the system that aligns with their production workflow.
Key recommendations for system selection:
- Define your welding method – Match the robot to your dominant welding type (MIG, TIG, spot).
- Consider cycle times – Higher production lines require faster, more robust robots.
- Evaluate space and layout – Not all robotic arms fit in tight or complex layouts.
- Software compatibility – Ensure the robot integrates well with your current systems.
- Scalability – Choose systems that can adapt if production increases.
By taking a systematic approach, companies reduce risk and maximize productivity from day one.
Common Mistakes in Robotic Welding Integration
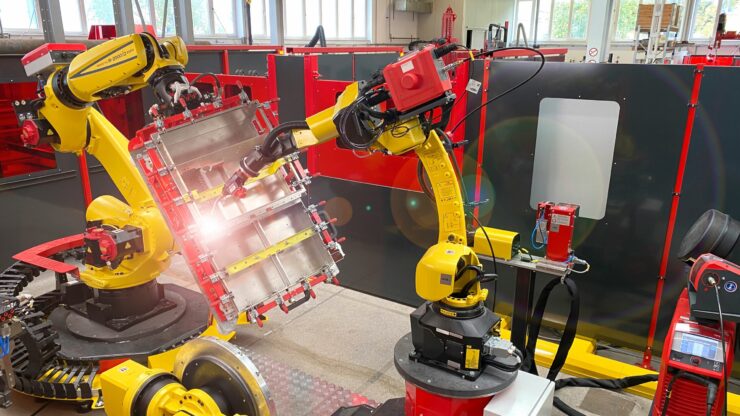
Even with the best tools, improper integration can lead to setbacks. Avoiding common errors during setup makes a major difference.
Top mistakes to watch out for:
- Skipping simulation tests – Failing to simulate real operations leads to misalignment and delays.
- Undertraining staff – Operators must know both welding principles and robotic controls.
- Ignoring maintenance plans – Robots require scheduled servicing to stay consistent.
- Assuming instant ROI – Results improve over time with proper monitoring and adjustment.
- Over-customization – Excessive tailoring can cause long-term limitations in flexibility.
Planning for long-term use rather than immediate gains results in sustainable output and fewer disruptions.
Evolving Role of Human Workers
Robotic welding does not eliminate jobs—it transforms them. Human roles shift from manual welding to supervision, programming, and system maintenance.
Welders are becoming machine operators and quality assurance specialists. Instead of repetitive tasks, they manage the robot’s performance and intervene during exceptions. With proper training, a workforce becomes more skilled, more productive, and more valuable.
Upskilling programs are vital. Companies that invest in employee education during automation transitions gain stronger teams and higher job satisfaction. Workers trained in robotic welding also gain access to better career opportunities across industries.
The Future Outlook
The future of manufacturing is undoubtedly shaped by intelligent automation. As technology advances, we can expect robot welders to become even more adaptable and intelligent—capable of real-time adjustments and self-optimisation. Companies that embrace this shift now are likely to gain a competitive edge as demand for faster, safer, and more precise manufacturing processes continues to grow.
In conclusion, integrating robotic welding into your production line isn’t just a smart move—it’s a strategic necessity for staying ahead in today’s manufacturing landscape.